Blow Moulding is a manufacturing process for moulding single-piece plastic objects in which a thermoplastic is extruded into a split mould and blown against its sides.
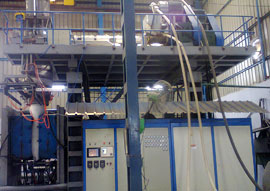
It is a plastic shaping process in which heated resin is clamped over a mould while positive air pressure blows the resin into its desired shape. It begins with melting down the plastic and forming it into a preform, a tube-like piece of plastic through which compressed air can pass. There are three main types of blow moulding – extrusion blow moulding, injection blow moulding, and stretch blow moulding.
They have following advantages:
- Economic on large scale productions
- Largely automatic process, less manpower
- High product durability (irrespective of raw material quantity)
- Latest technology